How the Papermill in Whangarei make beautiful paper from plant fibres and recycled cloth
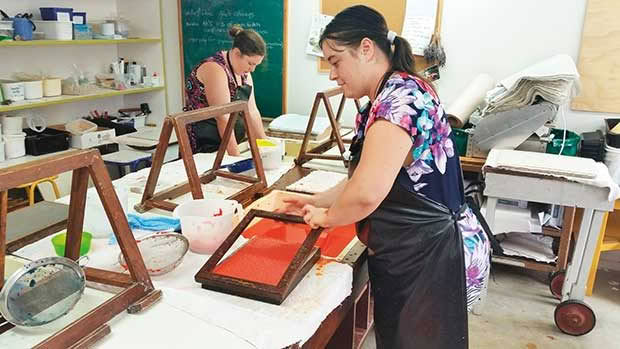
Julia making an orange paper at The Papermill.
There is something very satisfying about making your own paper.
Words: Jane Wrigglesworth
Paper-making is cathartic, but that’s not entirely why it’s so satisfying. It also provides you with a means of recycling the enormous waste of commercial paper that goes into our bins, and it’s surprisingly easy to do.
Blend small pieces of waste paper with water (an old food processor works well), pass a screen-like material through the mixture, blot away the excess water, then lay the paper out to dry. If you desire, you can add flower petals or herbs to the pulp, making something beautiful, scented and unique.
If you’re really serious about it, the paper can be calendered (pressed) to ensure the surface is smooth. There you have it, your own handmade paper.
You might be surprised to know what can be employed to create paper: wood fibres (from recycled paper), plant fibres (like flax and cabbage tree leaves), and even recycled cloth.
But Paula Lang from The Papermill in Whangarei says their unique papers use agapanthus vegetation, banana palm, toetoe and canna lily leaves, sometimes with the addition of grape skins, kauri chips and bits of fabric.
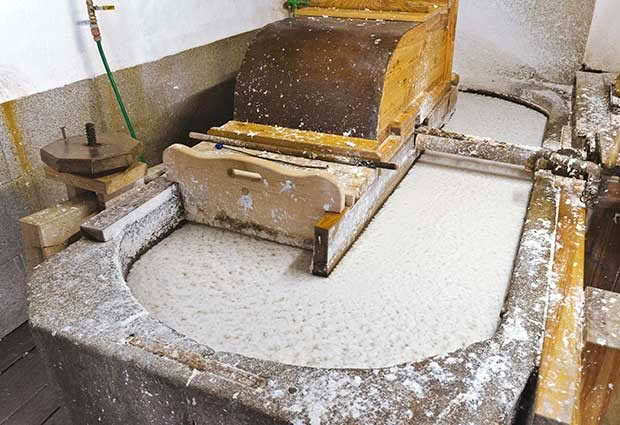
A Hollander beater machine uses paddles to mulch and ‘beat’ fibres into a slurry.
“Making paper from recycled paper (offcuts from local printing businesses) is the easiest. The paper is ripped up or cut up by hand and then mulched by hand with water.
“Making paper from plant fibre is more time-consuming and process-intensive. We have to harvest the plant, cut it up, boil it, and then mulch it finer through the Hollander machine (see below). But we find the most popular papers are recycled papers that have plant fibres or other inclusions added.”
Even old denim jeans. Google ‘paper made from denim jeans’ and it’s not as uncommon as you might think. This is where having a Hollander beater – a machine developed in 1680 to produce paper pulp from cellulose-containing plant fibres – comes in handy.
“First we get an old pair of pure cotton jeans,” says Paula. “They’re then cut up into very small pieces and soaked for weeks. It’s then boiled and soaked some more.
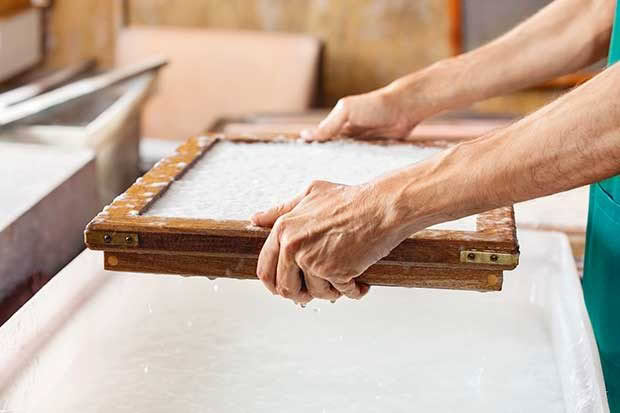
A mould and deckle holds the slurry, allowing it to dry and form a sheet of paper.
Finally, when the fibres have broken down a bit, it’s put through the Hollander to be processed some more. From start to finish it takes about three months to make the pulp.”
Using fabric as a material for making paper is not unusual says Paula.
“Historically paper has been commonly made with fabric remnants and rags in the western world since the 11th century. It’s only since the 1800s that paper has been consistently made from wood pulp.
As well as jeans, we make paper from hemp, cotton and silk fabrics. We enjoy experimenting with various materials.”
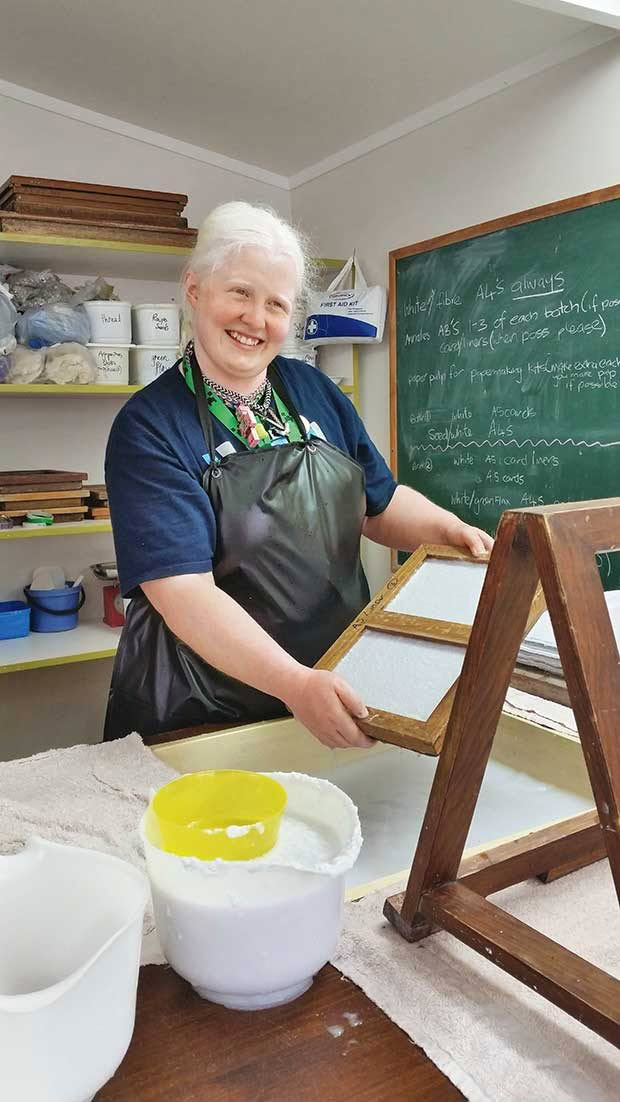
Nicole making card liners at The Papermill.
New Zealand flax (harakeke) makes an excellent medium for papermaking too. Marilyn and Marty Vreede from Pakohe Papers in Whanganui make handmade papers solely from flax.
“The majority of our papers are made using the flax that our local weavers can’t use,” says Marilyn. “It means that we are not in competition, and we provide a way for the weavers to dispose of their waste. Weavers drop off the offcuts, usually a fadge full, and take away an empty fadge for the next lot.
Occasionally we need to harvest ourselves, in which case we are careful to take from the great grandparents (the older leaves of the plant) and older.”
Permission is always sought first, says Marilyn.
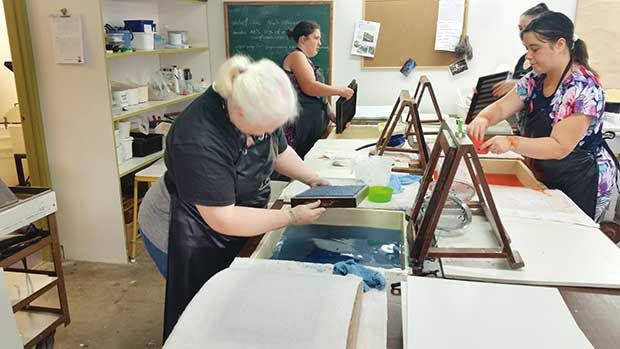
The Papermill studio.
“Each region has its own tikanga (protocols) when harvesting the harakeke,” says Marilyn. “The most important aspect is the karakia and asking permission before harvesting and making sure that the rito (centre) and the two sets immediately below the rito are left on the plant. Every other rau (leaf) is useful for paper making.”
Dry days are best for cutting and gathering, but if there has been recent rain, the flax is set aside to dry before processing.
The Vreedes have perfected six styles of paper after experimenting with more than 20. The papers are sold on their website, but they also make specialty papers for customers.
“Marty and I started making harakeke paper almost 14 years ago, possibly longer,” says Marilyn.
“It began as an after work and weekends project and we made quite a few varieties of papers. We had to cut down to the most popular papers, which is the range available today.”
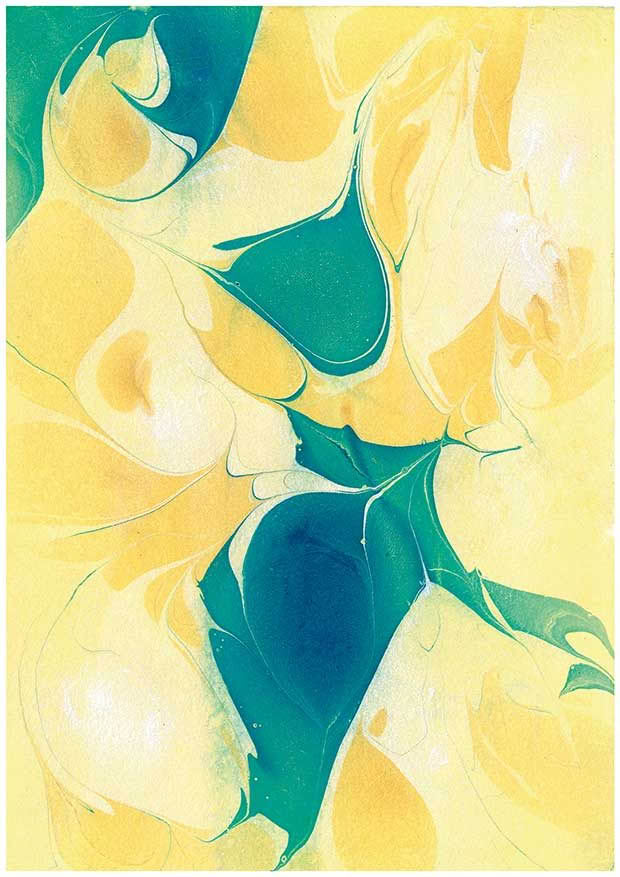
Marbled paper by The Papermill.
The papers are made from 100 per cent New Zealand flax fibre. In order to keep it as natural as possible, they decided to exclude sizing, which effectively makes their paper waterleaf, a type of unsized paper typically used for paper towels, tissues, and blotting papers.
“The papers are still perfectly suitable for photocopying and ink jet and laser printing of certificates, invitations, letters, documents, and fine art printmaking,” says Marilyn.
The process they use is a mix of Eastern and Western methods added to their own experience over the years. Marty designed and made all their equipment and they are always looking for new ways to improve production.
They run workshops for weavers (“which teaches them how to process the flax off-cuts into paper so there is no waste”) and others.
When it comes to papermaking, both Paula and Marilyn are in agreement that sharing what they’ve learned with others is a blessing.
“Making the paper is very therapeutic and a great way of team bonding,” says Marilyn. “We love teaching workshops and sharing the knowledge.”
Paula encourages everyone to give papermaking a go.
“Papermaking is something you can do at home (you can use your food processer to make mulch) and it’s a great way of recycling,” she says. “It’s a great activity with children too. Don’t overthink it and don’t be afraid to experiment.”
HOW FLAX PAPER IS MADE
Flax leaves are harvested and cut into small pieces, about 2.5cm square. The leaves are then boiled in caustic soda to remove the lignan which acts as a glue that connects the cellulose and hemicellulose within the leaves. Working with caustic soda can be dangerous, so protective gear should be used.
A stainless steel pot must be used as caustic soda will eat away at an aluminium one and give off flammable hydrogen gas.
The fibre is set aside to cool for a couple of days before being washed, then run through a blender to create an even texture, but a Hollander beater is ideal for commercial quantities.
Beating in the Hollander continues for about two hours, depending on the type of paper required: the finer the paper, the longer the beat.
The pulp can then be bleached if desired. A mould and deckle are immersed in the water and the fibre agitated to allow it to float above the mesh.
The mould and deckle are then pulled out, and the pulp sets on top to form a sheet of paper. Excess water is blotted off and the paper is dried. The paper can then be calendered (pressed) to make it smooth.
ABOUT THE PAPERMILL
The Papermill was established in 1989 by Rhondda Rutherford-Dunn as a space for intellectually, physically and emotionally-challenged people to build self-esteem, confidence and life skills through the process of papermaking.
Today it is a vibrant creative space where paper and paper art is created. The organisers hold an annual exhibition and create pieces for wearable arts events. Visitors are welcome (Monday to Friday 9am-3pm) and you can browse the various papers and products in the shop, and see the papermaking process firsthand.
The Papermill sells papermaking kits for $25, which includes a small mould and deckle, dried paper pulp, felts and sponges, and instructions.
www.thepapermill.co.nz
PAKOHE PAPERS
This family-based cottage industry is run by Marilyn and Marty Vreede. The couple say respect for the environment and the use and management of harakeke, one of the most treasured resources, is paramount.
“We consult and work co-operatively with local traditional weavers and use only the flax that they cannot use to make our paper. Together our aim is to ensure that the harakeke plants that provide our raw material are managed in a way that will ensure its availability for future generations.”
Marilyn and Marty run harakeke papermaking, letterpress and typography, and printmaking workshops throughout the year.
www.pakohe.co.nz
Love this story? Subscribe now!
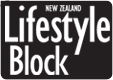